基于Hypermesh/Fe-safe的同步環組件疲勞壽命分析
2017-07-05 by:CAE仿真在線 來源:互聯網
變速器同步環組件是鎖環式同步器系統的重要組成部分,鎖環式同步器系統的一種主要失效模式為同步環外環的斷裂,而引起同步環外環斷裂的主要原因是齒套偏擺導致同步環外環局部受力過大。針對此問題,采用Hypermesh隱式分析來計算同步過程中齒套偏擺對外環的擠壓應力,并采用Fe-safe軟件以強度分析結果為輸入,進行同步環外環疲勞壽命分析。通過此分析,在同步器設計初期進行同步環外環疲勞壽命計算,根據計算結果進行結構優化,以滿足疲勞壽命設計要求。
疲勞破壞是工程結構和機械失效的主要原因之一,引起疲勞失效的循環載荷的峰值往往遠小于根據靜態斷裂分析估算出來的“安全”載荷[1]。因此開展同步環組件疲勞壽命研究對變速器同步器設計有著重要的工程意義。
1 簡介
目前廣泛采用的同步器是慣性式同步器,它有鎖環式和鎖銷式等形式。轎車變速器由于轉動慣量小,主要以鎖環式同步器為主[2]。鎖環式同步器主要通過同步環錐面碳層的摩擦來實現轉速的同步,使整個換擋過程平順完成。
理想狀態下,同步器在同步過程中同步環組件不會發生疲勞破壞。然而實際工況下,撥叉在撥環過程中,可能出現三個叉腳只有一個受力的情況,從而導致齒套偏擺,引起同步環外環局部受力過大,進而引起疲勞破壞。齒套偏擺狀況如圖1所示。
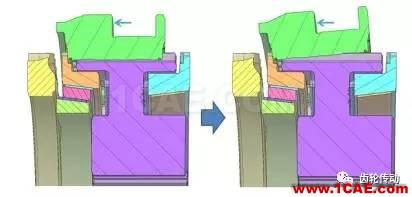
圖1 齒套偏擺示意圖
本文以某變速器雙錐同步環為例,基于Hypermesh/Fe-safe軟件進行齒套偏擺時同步環疲勞壽命分析,通過此分析,為同步器前期結構設計提供指導,確保其滿足設計要求。
2 強度分析
2.1 分析模型
在進行CAE分析過程中,前處理花費的時間占整個分析的60%以上,因此想要提高工程師的工作效率則必須選擇有效的、便捷的前處理軟件[3]。前處理過程主要包括:幾何處理、網格劃分、約束載荷施加及輸出參數設置。本文中的分析過程采用Pro/e軟件進行幾何建模,將Pro/e生成的.stp格式幾何模型導入Hypermesh軟件進行前處理。
為了節省分析資源的同時獲得較準確的分析結果,同步環組件采用二階四面體(C3D10I)及一階六面體(C3D8I)混合建模,為了保證計算精度和計算效率,根據以往經驗對應力不集中的地方采用較為稀疏的網格進行劃分,對應力集中位置采用較細密的網格進行劃分,對某些小倒角、小孔進行簡化處理,避免產生過小尺寸的網格單元。圖2所示為同步器系統的有限元分析模型。
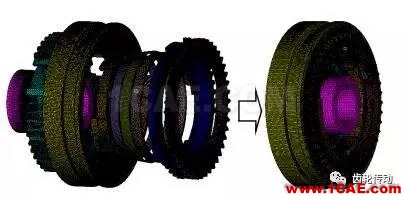
圖2 有限元分析模型
2.2 材料參數
在Hypermesh軟件中定義材料參數、建立結構屬性和賦予結構屬性,同步器系統各零部件的材料參數如下表1所示。
表1 零部件材料表
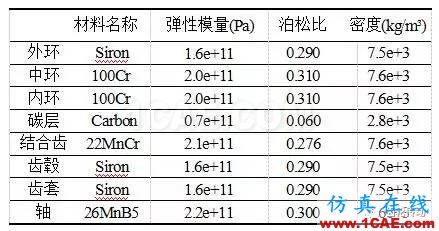
2.3 邊界條件與載荷
為實現齒套偏擺分析計算過程,本文采用在齒套上施加1000N換擋力的同時對齒套施加強制轉角的方式進行加載。由于外環結構為周向不對稱結構,換擋力的位置會影響外環應力分布。為計算外環的最大應力值及最小應力值進而分析外環的疲勞壽命,本文在齒套周向上每間隔24°角位置處設置加載點,每次在一個加載位置處施加F=1000N的換擋力,并對齒套施加一定強制轉角,進行應力計算,共計進行15次計算。換擋力分布如圖3所示。
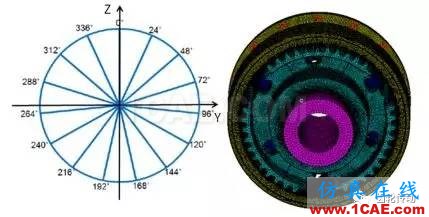
圖3 撥環力分布圖
變速器齒套最大偏擺角度為1°,分析過程中齒套施加繞Y軸和Z軸的強制轉角Yα和Zα,計算方法如下:
繞Y軸強制轉角Yα= Ycos(α)+Z sin(α)
繞Z軸強制轉角Zα= -Ysin(α)+Zcos(α)
其中:Y= 1°= 0.0174532925 rad
Z= 0°= 0.0 radα=0°、 24°、48°、……、336°
齒套施加繞Y軸和Z軸的強制轉角Yα和Zα的計算結果如表2所示。
表2 齒套強制轉角列表
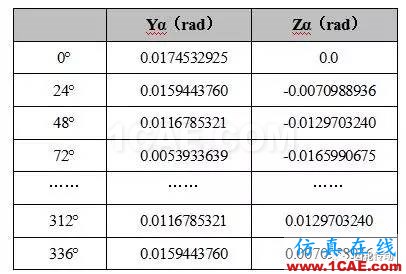
本文仿真分析加載過程共分為兩步,第一步在換擋力F作用下齒套和外環壓緊,第二步保持換擋力F不變,給齒套施加相應強制轉角。加載方式如圖4、圖5所示。
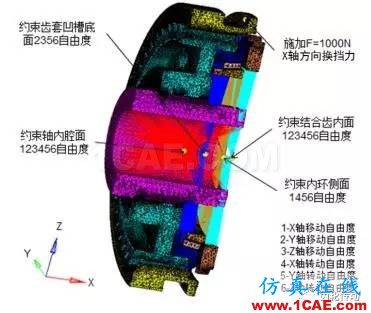
圖4 邊界條件及載荷(step1)
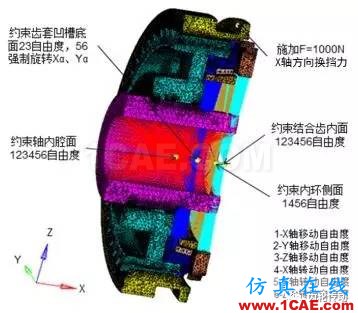
圖5 邊界條件及載荷(step2)
2.5 分析結果
將建立的有限元計算模型導入ABAQUS軟件中進行強度計算,獲得同步環外環在齒套偏擺情況下的強度結果,如圖6所示。
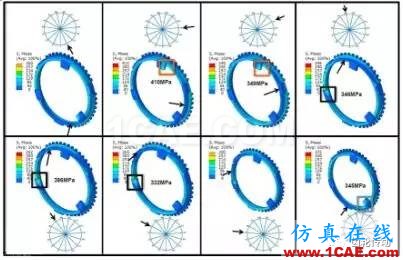
圖6 外環應力分布云圖
從圖6中可知,外環最大應力發生在換擋力施加在264°位置處,值為410MPa;外環最小應力發生在換擋力施加在96°位置處,值為185MPa。
3 疲勞分析
3.1 材料疲勞參數
材料的疲勞參數對同步器外環疲勞壽命的影響極大,外環材料疲勞參數如表3所示。
表3 外環材料疲勞參數表
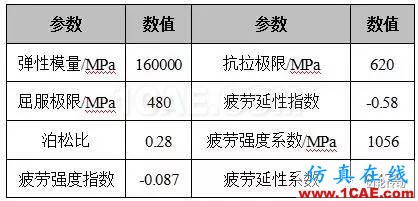
3.2 疲勞循環周期
同步器臺架試驗中,換擋過程外環平均轉速為1100rpm,平均換擋時間0.361s,因此整個換擋過程中,同步器外環旋轉6圈,承受6次交變載荷。同步器外環所在檔位換擋次數設計要求為65000次,疲勞循環周期如圖7所示。

圖7 疲勞循環周期圖
3.3 疲勞壽命分析
將外環強度分析結果,材料疲勞參數及疲勞循環周期輸入Fe-safe軟件中,采用最大主應力法作為應力判斷標準, Smith-Watson-Topper(SWT)作為平均應力修正方法,進行疲勞壽命計算。
3.4 分析結果疲勞分析結果如圖8所示,由圖可知,LOGLife小于零主要集中在卡爪根部(LOGLife<0不滿足設計要求),最容易發生疲勞破壞處LOGLife值為-1.1,循環次數N=10-1.1×65000=5163次。
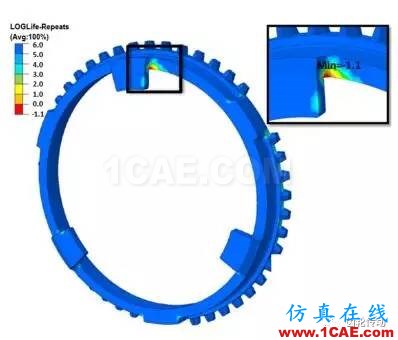
圖8 外環疲勞壽命云圖
經過疲勞耐久臺架試驗后,同步器外環出現斷裂,其斷裂情況如圖9所示,斷裂位置與仿真結果吻合。
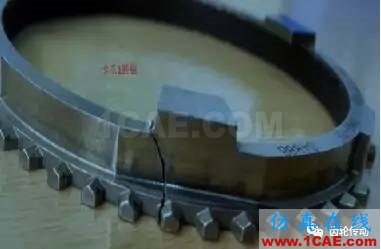
圖9 外環疲勞斷裂圖
(1)本文以某變速器同步器系統為研究對象,基于有限元軟件Hypermesh/Fe-safe,建立了分析齒套偏擺對同步環外環疲勞壽命影響的仿真分析模型;
(2)采用周向加載及強制轉角方式,通過強度分析計算,獲得了外環最大應力及最小應力分布位置及數值;
(3)結合具體試驗工況進行疲勞分析計算,獲得外環疲勞斷裂位置及疲勞循環次數;
(4)通過試驗與仿真分析結果對比,顯示斷裂位置與分析結果吻合。本文仿真分析方法可在同步器設計初期進行疲勞耐久預測,從而縮短研發周期,降低研發成本。
相關標簽搜索:基于Hypermesh/Fe-safe的同步環組件疲勞壽命分析 fe-Safe培訓 fe-Safe培訓課程 fe-Safe軟件培訓 fe-Safe在線視頻教程 fe-Safe教程 fe-Safe疲勞分析 Fluent、CFX流體分析 HFSS電磁分析 Ansys培訓 Abaqus培訓 Autoform培訓 有限元培訓