Dynaform汽車行業中的板材沖壓計算機仿真
2017-01-04 by:CAE仿真在線 來源:互聯網
前言
沖壓成形是一種歷史悠久的金屬加工工藝,隨著工業水平的不斷進步,沖壓技術和設備日益完善,已在汽車、航空、模具等行業沖壓加工占據著重要的地位。
眾所周知,汽車大部分構件都是薄板沖壓件,國外各大汽車廠商很早就開始采用計算機仿真技術用于指導產品的設計和制造。沖壓數值仿真的發展主要依賴于各種板成形軟件的涌現和進步,這些CAE 軟件大多可以利用CAD 生成的模型進行設計和工藝過程仿真,為新產品的開發提供參考依據。
DYNAFROM 軟件特點
DYNAFROM 集聚了美國三大汽車公司二十余年積累的豐富板成形仿真工程經驗,在程序中固化了大量經試驗驗證的專家經驗,對于不同成形工藝給出了最優的仿真參數如:質量比例參數、速度和阻尼系數等,大大降低對使用者的要求,成為模具及工藝設計人員的工具。其主要組成模塊如下:
· 前后處理模塊(Pre /Post)。
· 仿真工程模塊(FS)
· 模面工程模塊(DFE)
· 板料尺寸工程(BSE)
· 精確求解器模塊(LS-DYNA)
DYNAFROM 作為專業板成形軟件,致力于解決最復雜板成形工藝,廣泛應用于世界各大汽車公司、模具廠和高校以及研究機構。由于DYNAFORM 在現有板成形分析軟件原有的顯式基礎上增加了隱式分析功能,可以實現板成形從沖壓到回彈的完整工藝過程模擬,顯隱式分析做到無縫轉換,從而令板成形仿真更為便捷和高效。目前在國內長安汽車、南京汽車、上海寶鋼、中國一汽、上海匯眾汽車公司、洛陽一拖等知名企業得到成功應用。
DYNAFORM 應用實例
汽車設計的瓶頸是車身覆蓋件模具設計與制造周期,所關心的主要問題是由拉裂、減薄、環狀滑移線、起皺與回彈引起的工件缺陷。汽車裝配質量差的主要表現是車輛整體幾何形狀不精確協調。
仿真軟件的應用大大減少了試模的次數。奔馳公司采用前每套模具大致需試模3~4 次,采用DYNAFORM 后僅1~2 次就足以防止起皺和破裂。豐田汽車在引入DYNAFROM 后減少了模具設計和制造過程中46%的試驗工作。
下面簡單列舉兩個國內汽車企業利用DYNAFORM 進行工藝優化的工程案例:
· 案例1-國內某整車廠某車型前底板成形工藝優化
該零件采用原始工藝加工時,在成形過程中經常出現起皺、疊料及開裂問題,造成廢品率居高不下,嚴重影響了生產進度,增加了產品成本。
以下四個圖例顯示的是該零件原始工藝過程不同階段仿真變形特點:
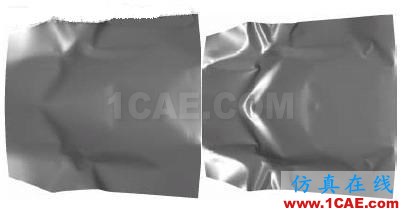
圖1、第一階段成形
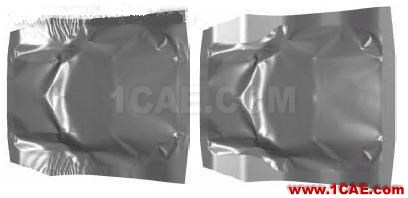
圖2、第二階段成形
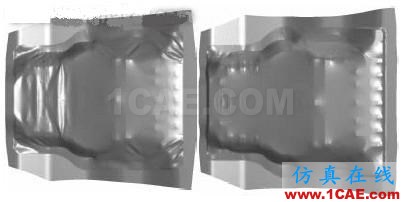
圖3、第三階段成形
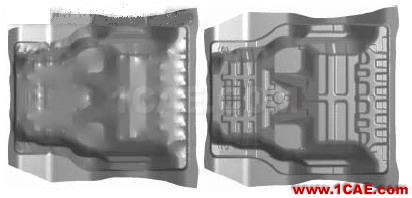
圖4、第四階段成形
針對該零件在成形過程中產生的上述缺陷,該廠模具工程師利用DYNAFROM 從以下方面去進行了方案改進及模擬仿真:
·調整拉延筋形狀和鎖模力解決局部裂紋
·調整坯料尺寸、增加材料的支撐、減小材料拉出延遲來解決起皺和疊料
·增加整形工序(如成形時增加角度和圓弧)徹底解決開裂問題
通過采用上述措施進行模擬優化,最終獲得了滿足設計要求的產品。如下所示。
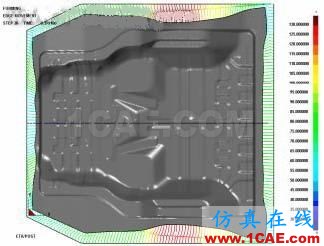
圖5、模擬優化后的產品變形及金屬流動
國內某整車廠輪罩成形工藝優化工程案例
該原始工藝成形過程存在的最大的問題是材料減薄不均,局部減薄過大,甚至造成局部材料破裂,降低了產品合格率,增加了產品成本。
以下三個圖例顯示了該零件原始工藝各階段零件變形特點:
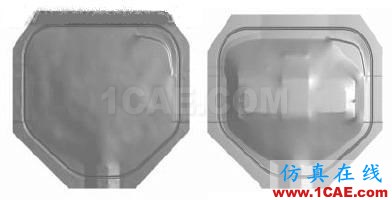
圖6、第一階段成形

圖7、第二階段成形
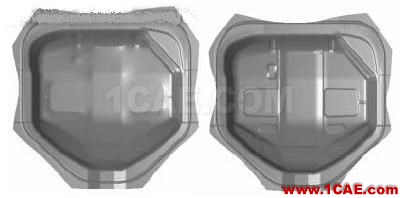
圖8、第三階段成形
針對該零件在成形過程中產生的上述缺陷,該廠模具工程師利用DYNAFROM 通過下列措施對上述問題進行了改進模擬:
· 調整拉延筋形狀、壓邊力和鎖模力改善成形狀態
· 調整坯料尺寸可以改善成形和節約材料
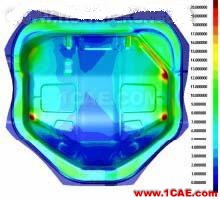
圖9、板料原始工藝產品減薄率
經過上述改進模擬獲得了優化后的產品,如下FLD 圖所示,產品各部分成形較為均勻,避免了材料的過度減薄的現象。
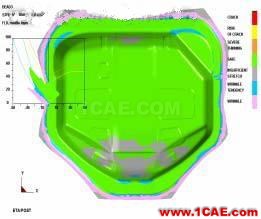
圖10、優化后產品FLD 圖
結論
由上述案例可知,利用DYNAFROM 軟件可以優化汽車覆蓋件的成形工藝,縮短模具設計和開發周期,降低開發成本并提高產品的質量。
相關標簽搜索:Dynaform汽車行業中的板材沖壓計算機仿真 Dynaform鈑金分析培訓 Dynaform汽車模具仿真分析培訓 Dynaform技術教程 Dynaform資料下載 Dynaform分析理論 Dynaform軟件下載 Fluent、CFX流體分析 HFSS電磁分析 Ansys培訓 Abaqus培訓 Autoform培訓 有限元培訓