沖壓成形工藝開發及量產成形改善新模式
2016-09-18 by:CAE仿真在線 來源:互聯網
隨著工業的不斷發展,模具行業數字化調試,已經成為不可逆轉的主流趨勢。前期成形工藝進行數字化模擬仿真運算,模具制作完成后量化成形性和與仿真運算的驗證一直是存在盲點。當成形能力極限檢測分析(FLD)技術從鋼材力學實驗逐步運用于沖壓成形穩定的時候起,有效的彌補了模具成形調試的量化缺陷。從方形的檢測網格到圓形的檢測網格,到后來圓點拍照掃描檢測。FLD的檢測手段和技術也在不斷的發展和進步,其涵蓋的數據量也越來越豐富,逐步實現了與前期仿真的模擬的數據平臺的構建。因此,本文主要講述目前FLD技術與CAE數據平臺構建、對比、調試運用和改善。
FLD、CAE各自優勢特點
FLD是通過材料杯裂實驗得到工程應力失效曲線作為材料成形能力極限依據。根據印制網格變化有效的觀察材料流動和應力變化。成形能力極限分析運用特點:⑴網格件壓制,可以清晰觀察晶格變化,判斷材料流動趨勢;⑵檢測材料厚度變化,根據臨界厚度和危險厚度,抓住調試重點;⑶晶格應變檢測數據反饋在成形極限曲線(FLC)中,直觀反應與失效曲線、臨界曲線距離,實現成形性數字量化。
AutoFormCAE模擬計算對于模具調試的運用特點:⑴工藝不變情況下進行虛擬調試;調整定位、更改材料尺寸、更改拉延筋強度等;⑵進行數模工藝更改后,驗證整改理論效果;⑶模擬結果中,可觀察到產品各處晶格應變和材料厚度的理論變化。
在模擬文件中通過成形能力極限圖的運用,可以提交預示出成形風險,如圖1所示。由此可見,FLD是從實際情況作出成形量化分析。CAE是從理論情況進行的數字模擬分析。兩者結合相互支持,得到理論和實踐構建量化平臺通過數字平臺的對比,可以快速找到調試方向,確定調試最佳更改量,有效量化更改效果。
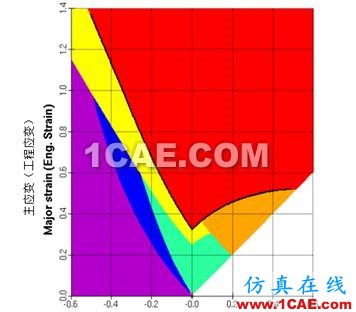
圖1 成形能力極限圖
實施案例一
江鈴某車型側圍內板在工藝開發初期,CAE模擬分析產品輪轂圓角處存在過渡減薄(材料減薄低于20%),有成形性風險,需要產品設計變更。產品工程師則認為后期模具調試可以實現。模具實際調試過程中,產品輪轂圓角出現了成形不穩定縮頸、破裂的情況,產品成形性需要提升。產品檢測的FLD圖,如圖2所示,型面上已經有成形危險點處于臨界區域。該點的應變狀態為拉伸應變。
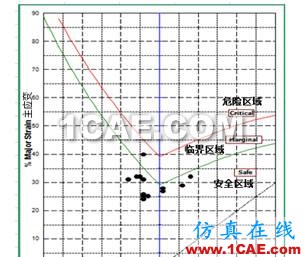
圖2 產品檢測的FLD圖
對材料使用潤滑油壓制拉延件進行FLD檢測。目前FLD檢測系統有兩種:通過Argus網格應變檢測系統進行網格拍照檢測;通過測量尺,做網格應變檢測。兩種方式各有特點:⑴人工檢測便于現場測量,直接指導現場調試,可以應對各種復雜區域檢測,產品網格存在輕微拉傷不影響產品檢測。缺點在于測量點數受到限制,只可關鍵部位測量,不是有經驗員工會存在檢測誤差;⑵Argus檢測系統,拍照自動識別檢測速度快,檢測精度穩定。缺點在于對網格的印制質量要求比較高,產品造形復雜區域拍照識別會受到影響。對與產品輕微拉傷和側壁,拍照網格識別存在困難,需要光照較好的條件下拍照,檢測結果要處理周期才能得出。基于以上原因本次產品的重點區域在R角尖點,人工檢測不存在檢測盲點,造形復雜的區域可以做多次細致測量。根據鋼廠提供的材料力學參數、FLC失效曲線,通過經驗公式計算可得到材料詳細的FLD圖,再通過拉延件網格測量按工程應力公式進行計算,得到產品檢測部位的網格應變極限情況。檢測數據危險點距離FLC曲線只有4%裕度。成形穩定性存較大風險。
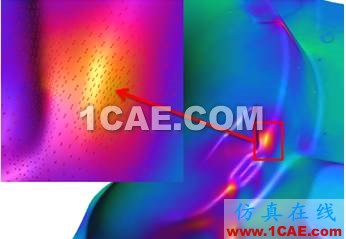
圖3 CAE的模擬分析結果
CAE分析結果如圖3所示,在輪轂處晶格應變均為平面應變,材料變化劇烈,易失效。成形性提升,須完成主應變減小,副應變為負(改變平面應變的情況)的應變調整。
相關標簽搜索:沖壓成形工藝開發及量產成形改善新模式 Autoform分析培訓班 Autoform汽車模具仿真 Autoform視頻教程 Autoform資料下載 在線軟件培訓 汽車鈑金代做 Fluent、CFX流體分析 HFSS電磁分析 Ansys培訓 Abaqus培訓 有限元培訓 Solidworks培訓