金屬粉末注射成型及Moldflow運用
2016-11-23 by:CAE仿真在線 來源:互聯(lián)網(wǎng)
一、概述
金屬粉末注射成型(MetalPowderInjectionMolding,簡稱MIM)技術是當今粉末冶金領域發(fā)展最快、最具應用潛力的新型粉末冶金近凈成型技術,被譽為當今最熱門的零部件制備技術,該技術是傳統(tǒng)粉末冶金技術與塑料注射成型技術相結合的產(chǎn)物在制備幾何形狀復雜組織結構均勻高性能的金屬零件產(chǎn)品方,尤其具有優(yōu)勢。
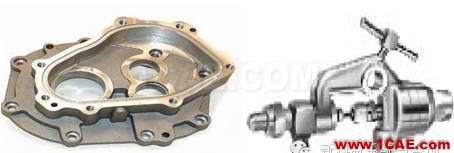
二、定義
金屬粉末射出成形是將細小、球狀的金屬粒子用各種不同的黏結劑混和并制造成小球的形狀成為射出料,再用射出成型機射出成型使用射出技術成形將金屬粉末,經(jīng)由射出機將其射入模具中成形,再將其冶金燒結成固體的技術成形后的生胚,需經(jīng)過脫脂的過程,把先前混入的黏結劑脫除,再經(jīng)燒結,即得密度95%以上之高密度、高強度的產(chǎn)品簡而言之,即以塑料射出的方式去生產(chǎn)金屬制品 。
三、優(yōu)勢
比常規(guī)粉末冶金工藝工序少,無切削或少切削經(jīng)濟效益高,克服了傳統(tǒng)粉末冶金工藝制品、材質不均勻、機械性能低、不易成型薄壁、復雜結構的缺點,特別適合于大批量生產(chǎn)小型、復雜以及具有特殊要求的金屬零件,MIM金屬粉末顆粒一般在0.5~20μm;理論上,顆粒越細,比表面積也越大,易于成型和燒結傳統(tǒng)的粉末冶金則采用大于40μm的較粗的粉末,傳統(tǒng)壓鑄成形強度低、精密鑄造無法大量量產(chǎn)、車削件成本較高等技術缺點 。
四、MIM技術發(fā)展
MIM技術發(fā)展已有一段時間自70年代末由美國開始,日本、德國等國皆先后投入研究八十年代初歐洲國家及日本都投入極大精力開始研究,并得到迅速推廣。特別是八十年代中期由于過去技術不夠成熟、原料成本過高、生產(chǎn)時間過長等原因,真正發(fā)展較為進步已是近年的事情已開始進入商業(yè)量產(chǎn)階段,在粉末冶金產(chǎn)業(yè)中被視為最熱門的金屬零組件成形技術之一。射出成型最大的優(yōu)勢是可以大量生產(chǎn)復雜的幾何產(chǎn)品,因各種設計需求,生產(chǎn)過程會運用到不同的塑料材料。然而,塑料材料無法滿足全部的設計需求,舉例來說,塑料就無法完全取代鐵的特性。粉末射出成型(PIM)為一獨特制程解決方案,因為能滿足形狀復雜且體積小的金屬/陶瓷精密產(chǎn)品大量生產(chǎn)的需求,目前正快速成長發(fā)展。到二零一二年時,全球粉末射出成型產(chǎn)業(yè)的產(chǎn)值會以每年成長15-20%速度擴張到一億五千萬美金,而根據(jù)Global Industry Analysts指出,到二零一七年時,產(chǎn)值會高達三億七千萬美金。粉末射出成型廣泛應用在許多產(chǎn)業(yè)上,其中陶瓷粉末射出成型主要應用在美國的醫(yī)藥和醫(yī)療市場;而在亞洲,金屬粉末射出成型則多半應用在消費性電子產(chǎn)品和信息科技方面。
五、技術挑戰(zhàn)
一般而言,粉末射出成型制程涵蓋四個部分:
1) 復合金屬和陶瓷粉末與高分子混合(又稱結合劑)來取得致密均勻的成型原料;
2) 成型原料經(jīng)過射出后形成生胚;
3) 去除結合劑之后,產(chǎn)生棕胚;
4) 燒結剩下粉末結構至成品雛型。
然而在射出成型階段,均勻的成型原料在注入模穴的過程中,卻充斥著許多亟待解決的技術挑戰(zhàn)。經(jīng)燒結后的成品缺陷往往是始于成型過程,例如:澆口殘痕、頂針痕以及分型線…等等,而這些缺陷很難在脫脂和燒結過程中去除。成型原料的選擇及模穴充填的粉末密度/濃度分布,更是會間接影響燒結階段產(chǎn)生收縮情形,進而引起表面瑕疵、內部結構缺陷、翹曲以及裂痕等問題。例如:燒結后易在融合線位置斷裂。
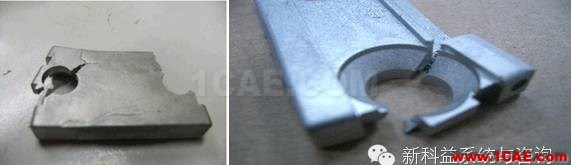
一般MIM制程采用材料:
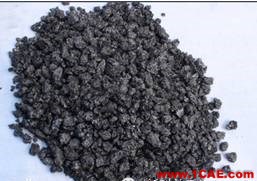
鐵-鎳-碳合金:Fe-2%Ni,Fe-8%Ni,不銹鋼合金:316L, 304L,630(17-4PH), 440C,420J2, 4140 特殊合金:M2,SKD11,Kovar(F150),Cu,SKH57,軟質磁性合金:Permalloy PB,Permalloy PC,18 Si-Fe.
六、材料特點
MIM射料大部分為遵循指數(shù)定律的擬塑性非牛頓流體,由于MIM射料中添加大量的金屬粉末,其熔膠密度相當高(約5 g/cm3),比容變化較一般塑料小。此外,MIM射料的熱傳導系數(shù)高,比熱較一般塑料低,于射出時黏度對溫度的變化會比較敏感 。
Moldflow材料庫含有MIM成型材料示意:
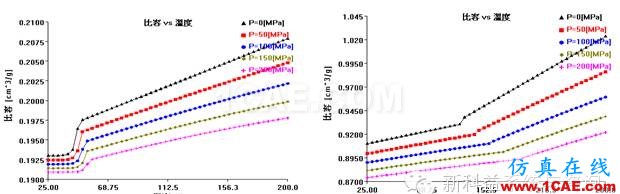
MIM產(chǎn)品的流動性模擬與短射實驗比對
流動模式驗證
1)澆口位置Jetting效果模擬
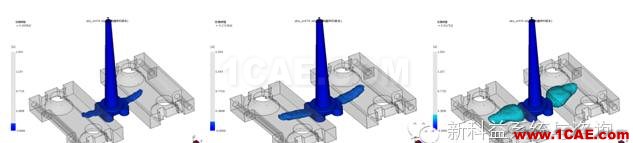
2)充填10%對比
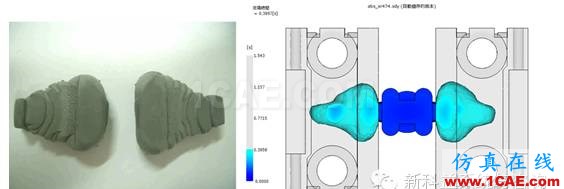
3)充填30%對比
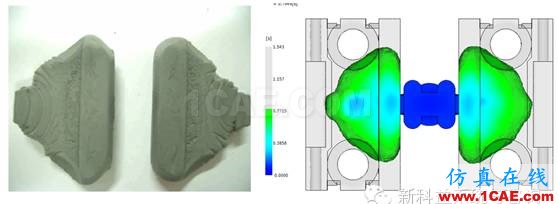
4)充填50%對比
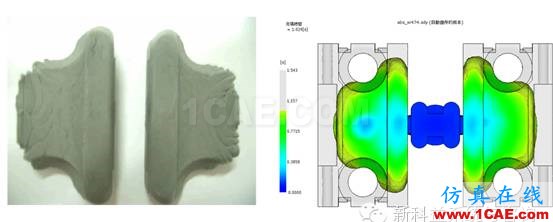
5)充填70%對比
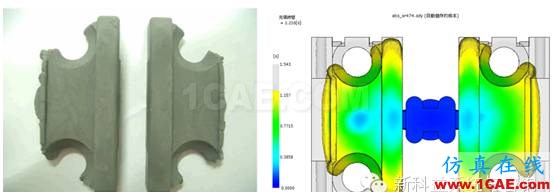
6)充填90%對比
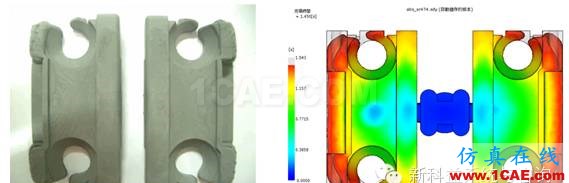
從Moldflow短射模擬可以看出,分析與實際流動模式能有95%以上的吻合。
七、斷裂改善對策
以上產(chǎn)品在燒結后易在融合線位置斷裂,對此,我們運用Moldflow模擬不同澆口的方案,改善過程如下:
改善方案1:薄膜澆口
● 熔合線移動至產(chǎn)品較厚的區(qū)域;
● 模具變更成本高且結構復雜;
● 澆口難于移除。
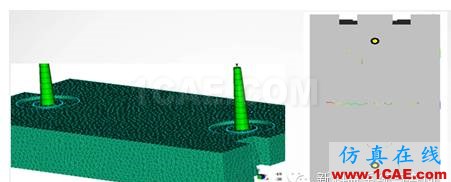
改善方案2:輪輻式澆口
● 熔合線移動至產(chǎn)品較厚的區(qū)域;
● 模具變更成本高且結構復雜;
● 輪輻式澆口會產(chǎn)生較多條熔合線;
● 澆口難于移除。
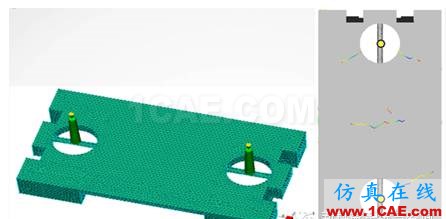
改善方案3:側澆口(2個)
● 模具結構簡單,變更成本較低;
● 生成三條熔合線;
● 澆口易于移除。
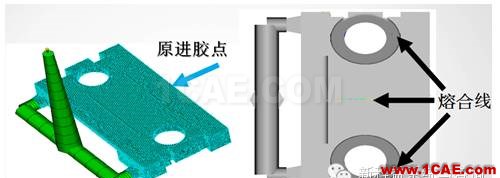
改善方案4:側澆口(2側)
● 熔合線移動至產(chǎn)品較厚的區(qū)域;
● 澆口易于移除;
● 產(chǎn)品中央易產(chǎn)生包封。
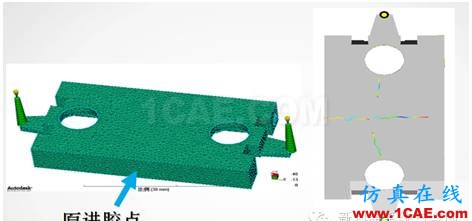
改善方案5:減少產(chǎn)品壁厚
● 為了避免嚴重的競流效應,減少產(chǎn)品中央的肉厚 ( 6.48 mm => 3.8 mm);
● 產(chǎn)品恐在燒結時扭曲變型,需準備相關治具于燒結時固定生胚。
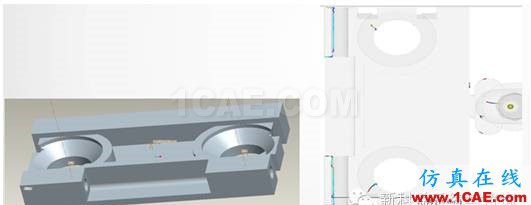
七、總結
1. 所選擇射料可準確的預測熔合線位置與相遇角度;
2. 模具設計變更方案建議采側邊雙澆口#1設計;
3. 經(jīng)廠商變更澆口位置后,MIM成品燒結后不再斷裂。
從以上案例可以看出因此在MIM成型前期運用Moldflow進行預測成型缺陷,并及時進行優(yōu)化具有非常重要的設計指導意義和經(jīng)濟意義。
相關標簽搜索:金屬粉末注射成型及Moldflow運用 Moldflow分析培訓 Moldflow課程培訓 Moldflow注塑分析的塑膠制品應用 Moldflow視頻 Moldflow技術教程 Moldflow資料下載 Moldflow分析理論 Moldflow軟件下載 Fluent、CFX流體分析 HFSS電磁分析 Ansys培訓 Abaqus培訓